SD4 Series - Double Seal Valves
SD4 valves are (double seal) safe flow valves designed for safe media separation applications in the food, beverage, dairy, pharmaceutical and chemical industries. It is available as a shut-off, change-over and tank bottom valve.
FEATURES
DELTA SD4 valves are (double seal) safe flow valves designed for safe media separation applications in the food, beverage, dairy, pharmaceutical and chemical industries. It is available as a shut-off, change-over and tank bottom valve. Other configurations are available on request. The DELTA SD4 valve is available as a shut-off valve in 4 standard housing configurations. Other configurations are available on request.
Advantages
- Leakage chamber arranged between the seat seals; the leakage chamber being forcibly closed (open valve) by the two leakage discharge valves (NO) or opened to the atmosphere (closed valve).
- Excellent hygienic characteristics primarily due to the ball-shaped housing without sump or dome.
- Profile seat seals providing crevice-free sealing and the compression of the seat seals is controlled by a metallic stop.
- Leakage discharge valves to drain the neutral area between the seat seals. The leakage discharge valves (activated together with main actuator) are also used as flush - enabling CIP and SIP cleaning of the neutral area.
- Actuator and control unit are standard parts from the SW4 product line. Additionally, a NOT element is fitted to the control unit as standard enabling to maintain higher line pressures.
How does the SD4 Double Seal valve work with leakage chamber ?
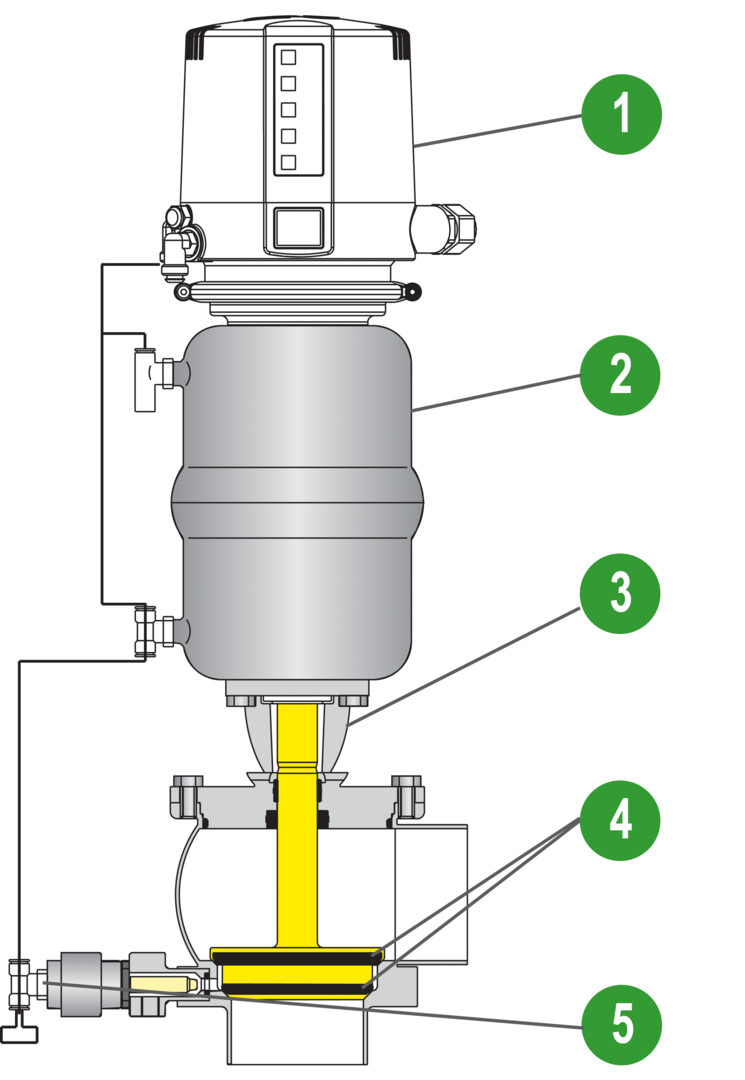
SD4 valves are used for safe separation of incompatible media. Safe media separation is provided by the two seat seal design.
A ring-shaped leakage chamber is arranged between the two seals. It is forcible closed or opened to the atmosphere by the two leakage discharge valves.
In case seat seal damage, the leakage will be drained through the leakage valves to the atmosphere and indicated.
- Control Unit
- Pneumatic Actuator
- Yoke
- Seat seals
- Leakage/CIP discharge valve