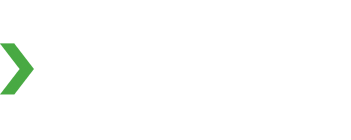
Triple-A® Spray Dryers
Industries : Dairy
Anhydro Triple-A Spray Dryers enable powder manufacturers to design and customize a complete drying solution for the production of free-flowing, dustless powders and agglomerates based on customer specifications.
Configurations:
- Single-stage dryer
- Multi-stage dryer
- Closed-circuit dryer
Options:
FEATURES
Based on a platform of innovative and advanced application technologies, the Triple-A Spray Dryer combines a new spray dryer design with an integrated fluid bed and an optional external fluid bed, providing our customers with total control over product quality and process efficiency.
Function and Principle of Operation
Triple-A Spray Dryers consist of five main components, all of which can be customized to meet individual requirements:
- Air distribution and nozzle atomization system
- Spray dryer
- Exhaust and fines recirculation system
- Second-stage integrated fluid bed
- Third-stage external fluid bed
The air distribution system delivers a constant airflow at a controlled temperature and volume into the spray dryer, integrated fluid bed, and optional external fluid bed. The nozzle atomization system ensures precise control over air distribution within the drying chamber, as well as powder particle and agglomerate sizes.
The spray dryer features a chamber design that ensures dust-free drying of a wide range of products, from low-fat to hygroscopic and "sticky" substances, leaving minimal product residue in the chamber. This design allows for significantly longer production times between CIP cycles.
The recirculation system utilizes cyclones, bag filters or a combination of both to recycle fines back into the spray dryer chamber, integrated fluid bed or external fluid bed. An integrated second-stage fluid bed is used for final, low-impact drying and cooling. The configuration is customized based on required capacity, residence time, temperature constraints, etc. An external fluid bed, including vibratory options, can be incorporated and connected to the integrated fluid bed outlet for additional drying and cooling.
Advantages
- Individually customized plants provide optimal solutions for specific process and production requirements.
- Complete process control, combined with uncompromising technology and engineering, ensures consistent end-product quality that meets predefined customer specifications.
- Equipment options are available for all capacity requirements, from small-scale plants to full industrial production.
- The innovative drying system design, along with easy service and maintenance access, ensures maximum production uptime.
- Consistently high yield, energy efficiency, and low operating costs provide rapid payback and a low total cost of ownership.
- Components and equipment are designed and engineered for reliability and performance, ensuring a long service life with minimal service and maintenance needs.
Special Features
- Innovative spray drying chamber for efficient drying and extended production times between CIP cycles.
- Nozzle atomization for optimal feed material spraying.
- Multiple air distribution options for complete airflow control.
- Various second-stage integrated fluid bed options for drying or cooling.
- Third-stage external fluid bed options for final drying and/or cooling.
- A selection of exhaust systems and fines recirculation options to ensure maximum product quality and yield.