STORIES IN THE MAKING
Ever try slurping down a milkshake that had a little too much shake, not enough milk? Thick, right?
Try as you might, your straw proves to be of little help, and you’ll probably opt for a spoon to enjoy the creamy dessert. Well, that’s what your process lines feel when pumping viscous product, because it’s so thick. The process line is full, and its parts are pushing product forward as best they can.
But what “spoon” will come rescue your product line?
The Complex Challenge
Products like fruit filling, pet food and liquid soap are viscous products that can be difficult to process. They make line cleaning a real challenge because clean in place (CIP) fluids often miss their lingering residue. This leaves room for bacteria growth, which jeopardizes the next batch process, and then that takes additional time to clean.
So now, not only did you waste residual product that could have made money, but you also wasted time by pausing production to flush clean in place (CIP) fluid.
We’ll use pet food as an example. According to this article, the pandemic has encouraged many pet owners to “stock up” on pet food, forcing companies to stock up on production staff. With all this demand, producers can’t afford to pause production lines. They need a “spoon.”
Our Sustainable Solution: Piggable Valves
Piggable valves help. They scrape the inside of process lines, removing thick, viscous leftovers. At the end of a product batch, a pig, which is a tight-fitting projectile, can be forced through the valve and pipeline. This recovers the residual product left in the line, allowing for greater product yield. Once the product is mostly recovered, the line can be flushed with little effort. This decreases CIP fluid usage, which lessens the need for chemicals, wastewater disposal, cleaning time, and it enhances plant capacity through increased productivity.
This cleaning mechanism also decreases the risk of cross-contamination. If no residual product remains, then they won’t mix with the next batch. That improves sanitation effectiveness and safety.
In short, we found your “spoon.” It’s called a piggable valve.
Watch them in action:
Driving high value and low life cycle costs, our solution makers recommend the D4 piggable valve for process line recovery. Now available in APV and Waukesha Cherry-Burrell brands.
Post Author
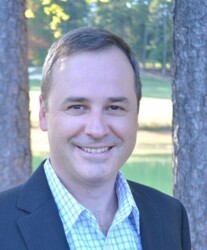
Global Product Manager, APV and Waukesha Cherry-Burrell Valves
Julien Bassett is the Global Product Manager for APV and WCB Valves, driving sustainable and innovative portfolio solutions across nutrition and health applications.
Contact Julien Bassett