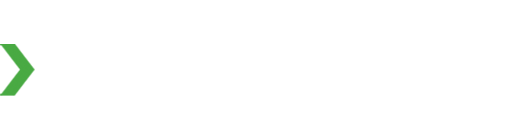
AutoBlend System - Continuous Production of Fabric Softener
Industries : Chemical
Fabric softener has been successfully marketed for many years and still shows high demand. However, since the introduction of biodegradable esterquats (EQ) the product boomed again.
FEATURES
Not only has the packing size been reduced from 5 liters to 1-1.5 liters to higher active matter concentration, but the market now demands up to 4 different perfume-color combinations. Using cationics, such as esterquat, allows the production of higher concentrations of active matter. Today the so-called 4-time-concentrate is usually used with approx. 20% active matter. Formerly the products, such as quarternary ammonium chlorides, allowed only up to 5% active matter, know as single-strength concentrate. Producing higher concentrated fabric softener with the traditionally used batch process causes major difficulties during stirring. As the molten esterquat is added to the warm water high viscosities occur so that there is a substantial increase in production time leading to a severe limitation in capacity. The modern alternative is continuous production with the BRAN+LUEBBE Master Batch and Finishing Process which has been developed with the worldwide leading manufacturers of esterquats. It has proven its favorable process behavior and is under continuous development. A typical B+L system for this application is shown in the flowchart. Molten esterquat, taken directly from the storage tank, is injected into softened water at elevated temperature. Preservatives can be added at this stage. These two components are thoroughly mixed in the pre-mix chamber of a PENTAX mixer and an electrolyte solution is added at the same time. The PENTAX is equipped with a frequency-controlled drive so that the mixing energy can be applied to the product in a controlled manner. This and the amount of electrolyte are essential for the final viscosity and the long-term stability. The resulting dispersion is cooled to approx. 25C before perfume, color and other additives are added. The final mixing can be performed either by static or dynamic mixing. This process step is open to the following options:
- Most effective energy use.
- Split into multiple B+L Finishing lines to produce more than one perfume-color combination simultaneously.
Effective energy use
- Using the necessary process water as coolant requires a heat exchanger as shown in the flow chart to recover the heat from the basic dispersion. As the flows are given by the capacity and formulation there is no control of the total flow. Thus about 70 80% of the heat can be recovered. To increase the water temperature to the level required by the process small amounts of steam are necessary. Final cooling has to be done in an additional heat exchanger using cold water.
- The other option is to split the necessary amount of process water in half, produce the dispersion with hot water in the PENTAX mixer, add the electrolyte and dilute with cold water in a static mixer. Final cooling has to be done in an additional heat exchanger using cold water.
The option applied is determined by the type of raw material, the local production conditions and the quality requirements and have to be decided individually.