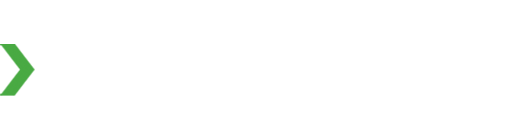
AutoBlend System - Continuous Production of Liquid Detergent
Industries : Chemical
Liquid detergents that contain a high content of soaps to mask the hardness of the water have conquered a substantial market share.
FEATURES
Liquid detergents that contain a high content of soaps to mask the hardness of the water have conquered a substantial market share. Normally washing powder contains silicates (e.g. Zeolith A) as softening agents. However, as they are insoluble in water it is nearly impossible to form a stable dispersion in the liquid detergent without using excessive amounts of dispersant. Therefore they are replaced in liquid detergents by soaps and non-ionics which have to be added to avoid deposit of calcium soaps on textiles and washing machines.
- LAS: Linear alcyl-benzene-sulfates as main anionic.
- FAS: Fatty alcohol-sulfates as anionic mainly used in detergents for sensitive fabrics and dishwashing liquids.
- APG: Alcyl-poly-glycosides as non-ionic which are biodegradable.
- Esterquats: Cationics that are mainly used in detergents for wool and fabric softener to avoid stiff fabrics after drying.
The demand for liquid detergents has increased steadily during the last years. This was very favorable for the manufacturers as the increasing energy costs have substantially raised the production cost for wash powder. So it became more profitable to manufacture liquid detergents. Therefore a wide variety of products are available for the consumer.
- General purpose liquid detergent.
- Liquid detergent specifically for colored fabrics.
- Liquid detergent specifically for sensitive fabrics.
- Liquid detergent specifically for wool.
These products differ in the formulation by using e.g. the following components:
- Enzymes like protease/amylase and lipase.
- Optical brightener.
- Antibacterial materials and disinfectants.
- Foam-reducing substances.
- Color protecting substances.
- Perfumes.
- Ethanol for viscosity control.
The Process Can Be Split Into Three Steps: Step 1Aqueous solutions, caustic and diluting water are metered and combined with sulfonic acid. The neutralization is nearly completed in a static mixer. Step 2 Fatty acid is added to the premix in a dynamic mixer and the intensive mixing as well as the exothermal reaction leads to a complete neutralization. The product has to be cooled before the heat sensitive additives are injected. Therefore a cooling loop with heat exchanger and high recirculation rate is installed. This is necessary to run the heat exchanger without fouling and at the same time pH value is trimmed to the required value. Step 3The other additives required by the formulation are injected in a dynamic mixer for final mixing and at the same time fi nal viscosity and pH are continuously measured and controlled. If necessary the end product is cooled to the filling temperature.All components are controlled by flow-meters and these production data are registered and stored.