Mixers Aftermarket
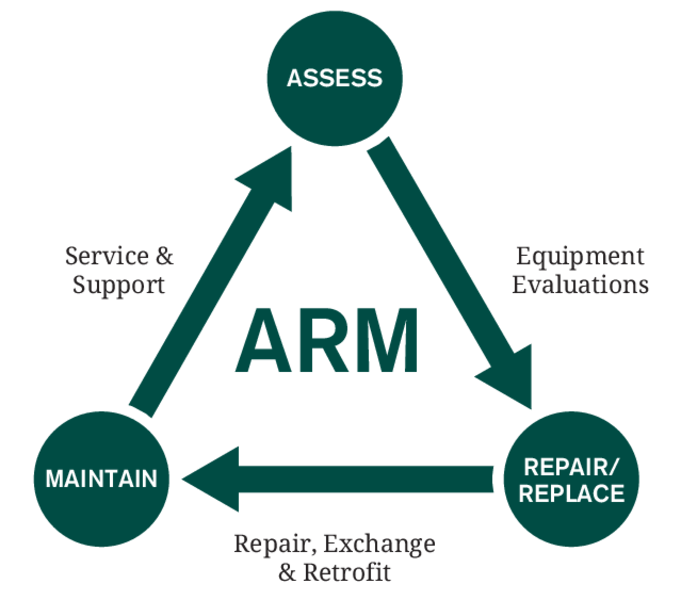
SPX FLOW offers a full spectrum of aftermarket support services that range from parts and technical support to full gearbox drive repacments and more. Because we want to be your preferred mixing partner, we apply an Assess, Repair and Maintain (ARM) process to optimize your equipment while maximizing productivity and uptime.
Assess: Utilize our MMR program, Field Services or Technical Support
Repair: Take advantage of our inspect & repair, replacement drive or parts services as well as premier service centers
Maintain: Future-proof your mixers with our maintenance & service program
Technical Support: Our applications engineers are ready to assist with common troubleshooting or emergency scenarios when and where you need it. Our team of experts are trained to handle your issues and get you back online. Fast.
RELIABILITY
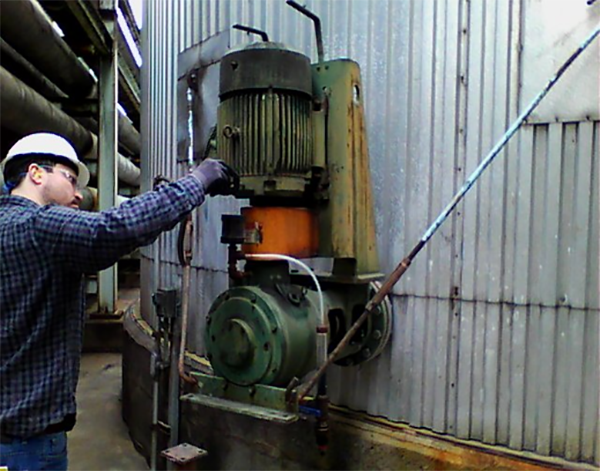
Mixer Modernization & Reliability
Optimize your equipment base and maximize productivity with a Mixer Modernization and Reliability (MMR) site survey and report. During the survey, our solution makers collect data from 30 key points for each of your mixers and then generate a customized MMR report onsite. The MMR report proactively identifies aging and at-risk equipment to minimize unplanned downtime.
If replacement is necessary, we identify similar equipment to help new maintenance personnel and reduce spare part inventory costs.
Our MMR program is designed to:
- Streamline and reduce spares
- Determine percent of investment vs. risk
- Identify potential savings of modernization vs. cost of delay
- Estimate cost of delay
Mixer Modernization & Reliability Learn More
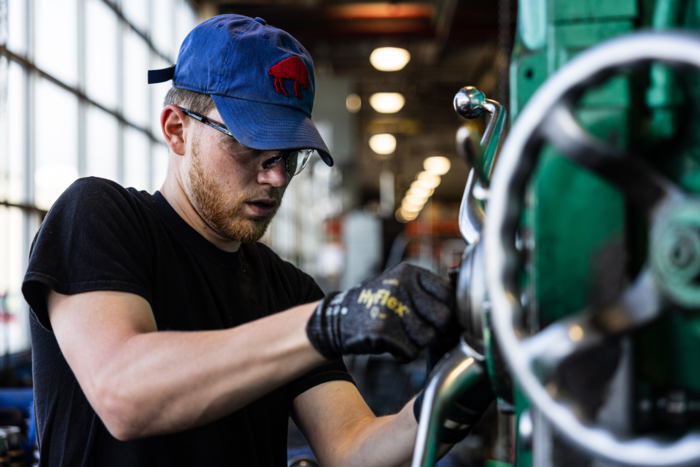
OEM SERVICE
Expert Service. Genuine Parts. Only from SPX FLOW.
Our vast network of Factory Service Centers provides the highest level of mixer maintenance and repair service available to ensure your mixer is ready to meet process demands with long and reliable service.
When serviced at one of our factory service locations, you will have peace of mind knowing that SPX FLOW has centuries of experience behind every interaction. Quality, convenience, responsiveness and reliability are all part of every service call.
Inspect & Repair
We are committed to providing the most comprehensive analysis and repair options available for top and side entry mixer drives. Our inspection and repair program provides:
- Increased reliability and dependability
- High-quality repairs meeting stringent specifications
- Extended life for your equipment
- Detailed reporting with tiered options for repair as well as warranty coverage
Our factory-trained technicians identify common problems such as:
- Engineer inspecting mixer drive
- Mechanical fatigue
- Upset conditions
- Shock load
- Process change
- Impeller balance
Gearbox ON DEMAND: Minimize Downtime. Maximize Readiness.
When operations can’t wait, SPX FLOW delivers. Our Gearbox ON DEMAND program is designed specifically for customers facing unplanned outages or urgent replacement needs.
We offer preconfigured gearboxes—available in a variety of ratios—that can ship in as little as 48 hours, with most orders fulfilled within 2 to 7 days. Each unit undergoes no-load spin testing prior to shipment to ensure performance integrity and is coated with our OEM standard paint system for lasting protection.
Please note: the gearbox includes the housing and internal components only. External accessories and attachments are not included.
All Gearbox ON DEMAND units are backed by our limited warranty:
- 12 months from installation or
- 18 months from shipment
(whichever comes first), covering defects in material or workmanship.
Need help identifying the right gearbox or have a breakdown situation?
Reach out to your SPX FLOW representative or customer support team for expedited support.
OEM SPARE PARTS
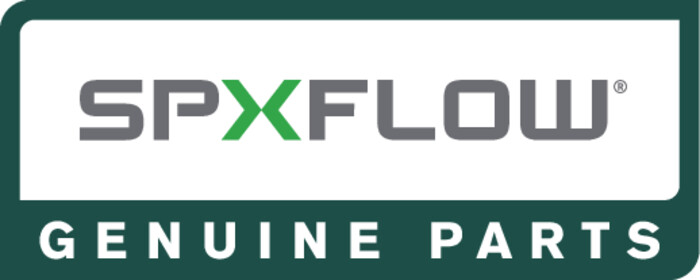
Genuine parts and maintenance kits
During Q4, when much of your focus is set on next year's planning, it’s important to remember that success next year starts now. Budget surplus this quarter can ensure things run smoothly in the year to come. With regular preventative maintenance and genuine OEM parts, your mixer equipment will be ready to perform throughout the year for more uptime and optimal performance.
Our mixer genuine spare parts are precisely engineered to our continuously increasing quality standards. As spares availability is crucial to the smooth running of your operation, our strategically located Spare Parts Distribution Centers and network of distribution partners offer rapid delivery of our genuine spare parts along with advanced spares consolidation and management services to help keep your processes running. Maintenance kits are also available, conveniently putting all the parts required for regular servicing in one kit, making it easier to service.
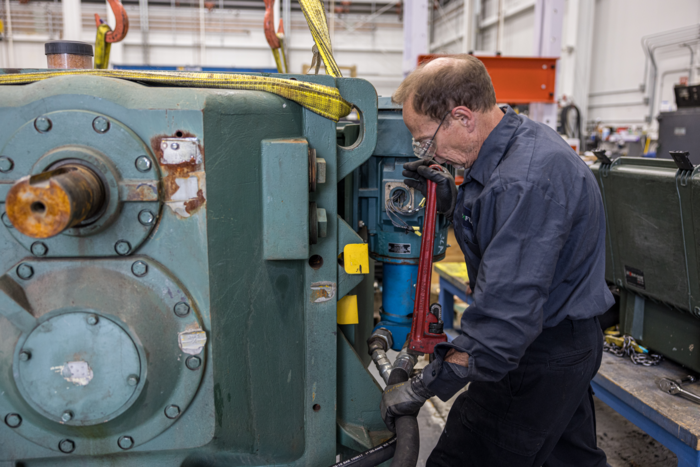
REPLACEMENT & RETROFIT
SPX FLOW has a long history of mechanical engineering and process design excellence. With brands like Lightnin, Plenty, and Philadelphia Mixing Solutions, to name a few, as part of our mixing solutions portfolio, our experience extends beyond designing and building new systems, we also know why drives might fail. Our Replacement Drive Support program for mixer and agitator drives follows these steps:
- Collect the mixer performance and the operational history of the unit to be replaced.
- Take into account the unique loads that mixing and agitation impose on a gear drive system.
- Consider process changes since the original installation.
- Analyze the in-tank parts design with reference to the current process in the tank.
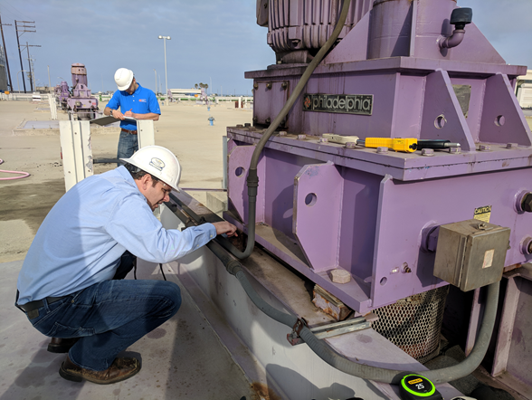
FIELD SERVICES
Our dedicated team of solution makers offer a range of onsite services to assist in your mixing operations. These include:
- Commissioning – Verification of proper installation and equipment startup.
- Onsite Consulting & Repair – Diagnostic services with onsite repair services.
- Preventative Maintenance– Diagnostic services at your plant location to ensure peak performance.
- Turnkey Services– SPX Flow offers a range of removal and installation services for our mixing equipment.
- Training– Comprehensive training so your team learns how to properly operate, maintain, and care for equipment.
- Maintenance & Service Programs– Comprehensive maintenance and service packages to accommodate specific customer needs.