Products
- Analyzers
- Automation Systems
- Butter Equipment
- Centrifuges
- Cleaning-in-Place Systems
- Deareators
- Draught Regulators
- Dryers
- Evaporators
- Fat Crystalization Equipment
- Filters & Strainers
- Heat Exchangers
- Homogenizers
- Membrane Filtration Systems
- Microparticulation Systems
- Mixers & Agitators
- Pasturization Systems
- Pigging Systems
- Plumbing Products
- Pumps
- Recreational Marine Products
- Spin Flash Dryers
- Spray Dryers
- UHT Systems
- Valves
- Adhesives & Sealants
- Automotive Heating System
- Baby Food
- Bakery Filing Cream
- Beer, Cider, Wine & Spirits
- Biodiesel
- Boats & Watercraft
- Building Infrastructure
- Butter & Spreads
- Cement
- Cheese
- Chocolate
- Coffee & Tea
- Condiments, Sauces & Soups
- Cosmetics
- Dairy Powders
- Ethanol
- Flavors & Fragrances
- Fruit Juice
- Fuel Supply System
- Hair, Nail & Skin Care Products
- Ice Cream
- Inorganic Chemicals
- Margarine & Shortening
- Meat & Animal-Based Proteins
- Milk & Cream
- Neutralization
- Nutraceuticals
- Oral Care
- Paints & Coatings
- Petrochemicals
- Pipelines
- Plant-Based Food & Beverages
- Plastic & Resins
- Refinery
- Soft Drinks
- Solvents & Solutions
- Specialty Chemicals
- Synthetic Rubber
- Yogurt
Water and Wastewater Treatment
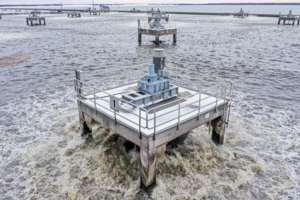
SPX FLOW offers advanced water and wastewater treatment solutions designed to meet the rigorous demands of industrial and municipal treatment facilities worldwide. Leveraging decades of expertise, SPX FLOW provides high-efficiency mixers and pumps specifically developed to improve operational reliability, reduce costs and optimize sustainability for water treatment applications. Our technology is essential for critical processes, from aeration and sludge treatment to chemical dosing, all backed by dedicated service and genuine parts to maximize equipment lifespan.
With our robust product portfolio—including the Raven 3800 Series Mixers Lightnin Series 700/800 High Torque Mixers, andJohnson Pump CombiFlex Series—SPX FLOW ensures process precision and compliance with water treatment standards. By collaborating with our team, site managers and engineers can access cutting-edge solutions that increase uptime and operational consistency, aligning with their facility’s sustainability goals and performance standards.
Why Choose SPX FLOW for Water & Wastewater Treatment?
SPX FLOW distinguishes itself through innovation, reliability, and a focus on process optimization. Our in-depth process expertise, coupled with advanced R&D facilities, enables us to customize solutions for your specific treatment needs. With SPX FLOW, you benefit from:
-
High-Efficiency Equipment: Proprietary impeller designs, such as the Talonâ„¢ low-speed surface aerators, maximize oxygen transfer and mixing with lower energy costs.
-
Reliability and Durability: Genuine SPX FLOW parts and certified technicians ensure our equipment offers consistent, long-term performance.
-
Sustainability and Cost Savings: Energy-efficient designs reduce overall operational costs and help meet environmental objectives.
Key Products for Water & Wastewater Treatment
- Engineered for harsh environments, this mixer provides long-lasting, reliable service with minimal maintenance needs, thanks to its self-lubricating design and drywell technology that prevents oil leaks
-
The PVE Series delivers heavy-duty performance with adjustable impeller locations, making it adaptable to fluctuating treatment conditions while minimizing downtime
-
With a design built for high torque and durability, the Series 700/800 mixers are ideal for sludge and aeration applications, providing quiet operation and long bearing life to withstand rigorous usage.
-
Known for a superior balance of value and performance, the Series 10 is perfect for mixing and flocculation, simplifying maintenance with fewer moving parts
-
These pumps are specifically tailored for efficient liquid transport, minimizing energy consumption across water treatment applications
Â
Water & Wastewater Treatment Applications
-
Aeration: Systems like the Talonâ„¢ Low-Speed Surface Aerator and GDX Impeller improve oxygen transfer and reduce operational costs in both atmospheric air and high-purity oxygen environments.
-
Sludge Mixing: Ensuring uniform mixing and preventing solids from settling, the Raven Series is suited for sludge holding tanks, digesters and equalization basins.
-
Chemical Dosing: SPX FLOW’s mixer drives, such as the PVE Series, allow precise chemical blending, minimizing waste and improving the reliability of flocculation, disinfection and pH control processes.
-
Lagoon Treatment: Our Raptorâ„¢ Directional Aerating Mixer is designed to increase dissolved oxygen while controlling odor and reducing energy costs in lagoon systems.
-
Effluent and Transfer Pumping:
-
Johnson Pump CombiNorm Series Centrifugal Pumps: These pumps are designed for high-efficiency fluid transfer in water and wastewater systems, handling clean and slightly contaminated liquids. The CombiNorm series is highly effective in effluent pumping applications, moving treated water safely to the next stage or final discharge point.
-
Johnson Pump CombiFlex Series Vertical Centrifugal Pumps: Built for reliability in demanding conditions, the CombiFlex pumps are well-suited for transferring water within multi-stage treatment processes, ensuring stable flow rates and reducing downtime in critical applications. These pumps are known for their versatility and ability to handle variable flows and viscosities, commonly required in water and wastewater treatment settings.
-
Johnson Pump CombiChem Series: For corrosive or high-temperature fluids often encountered in wastewater treatment, the CombiChem Series pumps offer enhanced chemical resistance and are designed for the rigorous demands of applications like dosing corrosive chemicals or moving aggressive waste streams. Their robust construction and material options make them an optimal choice for water treatment facilities dealing with challenging fluid characteristics.
-
-
Raw and Recycled Water Transfer: The Johnson Pump CombiFlex and CombiNorm Seriesprovide reliable performance for moving raw or recycled water between treatment stages. These pumps ensure consistent flow rates and energy efficiency, critical in handling large volumes in provide reliable performance for moving raw or recycled water between treatment stages. These pumps ensure consistent flow rates and energy efficiency, critical in handling large volumes in municipal and industrial water recycling processes
Â
Optimize Your Water Treatment Process with SPX FLOW
Achieve operational excellence and sustainability in water and wastewater treatment with SPX FLOW’s innovative mixers and pumps. Contact our team to discuss tailored solutions that enhance efficiency, reliability and environmental impact.
Â
Â
PRODUCTS
VIDEOS
Reliable Water Supply in Midden-Drenthe: How SPX FLOW Johnson Pumps Ensure Quality Drinking Water
CombiBloc Pump Overview: For Pumping Chemicals | Johnson Pump
CombiNorm Pump Overview: Efficient and Maintenance-Friendly Water & Chemical Pumping Solution
CombiFlex Universal Vertical Pump Overview: Rotatable Suction Bend & Easy Maintenance
FREQUENTLY ASKED WATER & WASTEWATER TREATMENT QUESTIONS
Our impeller technology, such as the Talon™ and GDX systems, is designed for efficient oxygen transfer and mixing, reducing energy consumption by up to 25% compared to traditional designs.
When selecting a mixer for aeration, it’s essential to consider the oxygen transfer rate required, the tank or basin size, the type of wastewater, and the required mixing intensity. Additional considerations include power efficiency, impeller type, and the mixer’s ability to handle variations in oxygen demand to maintain consistent dissolved oxygen levels.
Impeller selection should be based on the type of aeration process and desired outcomes. For surface aeration, low-speed surface impellers like the Talon™ are ideal for maximizing oxygen transfer. Submerged aeration applications, such as with the GDX impeller, work well for fine bubble dispersion and are suited for tanks that alternate between aerobic and anoxic processes.
Ragging occurs when fibrous materials accumulate on the impeller, increasing the load on the motor and potentially leading to motor overload or component failure. It also disrupts the mixing process by obstructing flow and reducing efficiency. Anti-ragging impeller designs, like the ARI-2 and GDX impellers, prevent material build-up, ensuring consistent mixing performance and reducing maintenance needs.
Anti-ragging impellers are designed with features that prevent fibrous material from accumulating, which can compromise mixing performance. Impellers such as the ARI-2 are specifically designed to disperse flow away from the impeller shaft, minimizing contact with ragging materials and reducing the need for frequent shutdowns to clear blockages.
Proper impeller placement ensures optimal oxygen distribution and prevents short-circuiting within the tank. For example, placing the impeller closer to the surface can improve oxygen transfer, while positioning it lower in the tank promotes better circulation and reduces dead zones. Adjusting impeller height can also improve the system’s ability to handle varying load conditions effectively.
Power efficiency is crucial for minimizing operational costs, especially in continuous processes like aeration. Choosing mixers and impellers with optimized power consumption, such as low-speed, high-torque mixers, can significantly reduce energy use without compromising performance. Energy-efficient impellers like the Talon™ or GDX provide effective aeration with less power input.
Mixers designed for easy maintenance, with features like drywell designs and self-lubricating components, reduce downtime and minimize maintenance costs. Additionally, mixers equipped with inspection windows or quick-release parts facilitate on-site servicing, keeping operational interruptions to a minimum.
SPX FLOW provides mixers like the Raven Series and PVE 12-16 Series, which ensure effective sludge mixing and help maintain a consistent flow, preventing settling in holding tanks and digesters.
VFDs allow for adjustable mixer speed, enabling precise control over mixing intensity to match varying oxygen demands. This flexibility is particularly beneficial in aeration processes that fluctuate with changing loads, allowing operators to reduce speed during low-demand periods and conserve energy without sacrificing aeration efficiency.
Retrofitting is beneficial when operational efficiency drops due to frequent clogging or when maintenance needs are high. Anti-ragging impellers can be fitted to existing systems, enhancing durability and reducing downtime. Facilities with high fiber content in wastewater, such as municipal plants, may benefit significantly from retrofitting to maintain consistent aeration.
Tank dimensions directly impact mixer power requirements, impeller size and positioning. Larger tanks may require multiple mixers or specialized impellers to ensure uniform mixing and adequate oxygen distribution. Consulting with mixer experts can help determine the right combination of mixer and impeller based on tank geometry and process requirements.
When selecting a centrifugal pump, it’s important to consider the fluid characteristics (such as viscosity and corrosiveness), required flow rate, total dynamic head, pump material compatibility and the specific application needs. Choosing the right model and material for the application ensures reliability and reduces maintenance over time.
Vertical centrifugal pumps, such as the CombiFlex Series, are ideal for applications where space is limited or when handling wastewater with some solids. These pumps are designed to save space, improve stability and often provide easier access for maintenance. They also help reduce the risk of leakage when handling large volumes in wastewater treatment systems.
Pump efficiency directly affects energy consumption, which can be significant in continuous operations like water treatment. High-efficiency pumps, such as those in the Johnson Pump® CombiNorm Series, reduce energy costs by delivering the required flow with less power, which is especially beneficial in large-scale treatment facilities with long operating hours.
Cavitation occurs when vapor bubbles form in the pump due to low pressure, causing potential damage as they collapse. It can be prevented by ensuring proper pump sizing, maintaining adequate suction head, and avoiding excessive flow rates. Selecting a pump with appropriate net positive suction head (NPSH) requirements, such as the CombiChem Series for challenging fluids, helps mitigate cavitation.
Regular maintenance, including inspection of seals, lubrication of bearings and monitoring for unusual vibrations or noise, helps extend the life of centrifugal pumps. For wastewater environments, using genuine spare parts and implementing preventative measures like strainers to filter out solids can reduce wear and improve pump reliability. Many SPX FLOW pumps are designed for easy maintenance to minimize downtime.